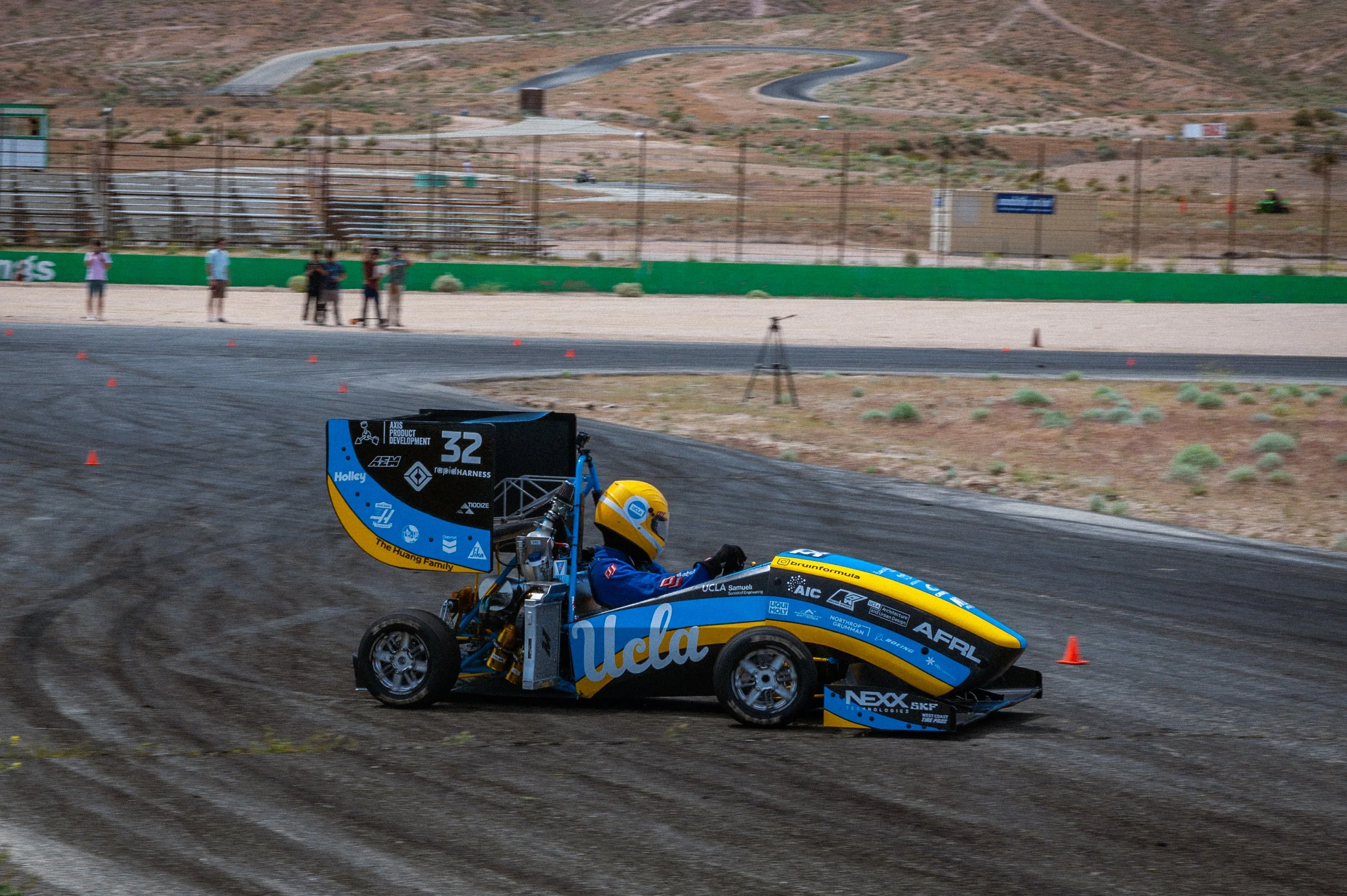
Bruin Formula Racing
Technical Director - Cockpit & Electronics (May 2023 - June 2024)
Controls Responsible Engineer - Shifting (June 2022 - May 2023)
Controls Manufacturing Lead (June 2021 - June 2022)
Controls & Electronics Member (September 2020 - June 2021)
Los Angeles, CA
2020-2024
Mechanical Design, Vehicle Controls, Machining, Manufacturing, Electrical Design, Technical Program Management
I joined BFR in my freshman year during the COVID-19 pandemic. On the team, I focused primarily on the Controls & Electronics subteams. For my freshman through junior, my main focus was on the design of a pneumatic shifting system, which was successfully implemented on Mk8, competing in May of 2023. In my senior year, I was one of two technical directors, leading the change from an IC to an EV vehicle platform.
As the technical director for the team, my role focused on the Cockpit and Electronics subteams. The team took a major transitional year from internal combustion cars (from Mk. 1 to Mk.8) to our first fully electric vehicle (Mk. 9). My role spanned integration, systems engineering, and technical project management. I developed tools in Notion for project management, system requirements, and parts tracking. I also led the High Voltage safety program for our team to manage and reduce risk around power electronics. On the hands-on technical side, I designed the physical packaging for the LV system, troubleshot and repaired electrical harnessing problems, and tuned the inverter parameters for optimal motor performance. The team was unable to complete the technical inspection at the competition due to the number of new components but still placed 37th of 75 teams due to our strong score in static events.
In my third year, I held the role of Controls Responsible Engineer on the shifting subsystem, but the role was more multifaceted than that title. I helped co-lead the controls subteam and worked on the Driver Safety subsystem. In the process of designing for pneumatic shifting, I led multiple members and worked across subteams to make sure the system integrated as flawlessly as possible and improved driving ergonomics. The shifting system ran without failures in the 2023 Michigan May FSAE competition, resulting in a 0.19s reduction in acceleration time, as well as a team-best 10th place (out of 112 teams that scored points).
Vehicle Integration and Testing
A major strength of mine is my ability to quickly troubleshoot and fix problems. With Mk7 this primarily entailed minor control fixes. Mk8 & Mk9 this scope increased immensely.
My primary goal with Mk8 was to validate and optimize the pneumatic shifting system. Competition was the crux of all this effort and two major fixes had to be implemented on the fly. The first was that shifting was not working during the first 3 accel runs. Before the final run, we made the snap judgment call to make a significant code change that would reduce data collection, and change tuning parameters. This led to the best run time of 4.67s. The second was when the tank blew out the evening before endurance. I was able to find a local paintball supply store quickly and communicate the issue, leading to the issue being fixed and us being able to run and finish endurance in 5th place, leading to an overall finish of 10th out of 120 teams.
On Mk9 my goal was to have a complete, running car which was a rules complaint. Due to delays in acquisitions, the timeline of power electronics integration was significantly shortened. Major contributions included building and fixing PCBs, function testing discrete components, integration testing the wire harness with functional groups in mind, and significant effort in the tuning of the vehicle controller and inverter. Through this process, I was constantly cross-referencing the rulebook and leading conversations on solutions to increase the odds of success at technical inspection.
Project Management
It is often said that FSAE is not an engineering competition but a project management competition. Working with large teams (in our case a team of 50 to over 100) can lead to communication challenges and significant integration challenges when subteams realize that their designs don’t integrate either with other subteams or with the overall vehicle goals.
To combat a lot of these project management issues I introduced tools, primarily using Notion for project management, requirements traceability, parts tracking, and safety. The tools were designed to manage the assignment of responsibility to members and track their progress within tasks. This can be viewed in multiple ways both through tables, boards, and calendars allowing for ease of use.
The requirements traceability is designed to track system goals from the top vehicle level down to individual components. This was helpful to make sure design criteria set early are verified in the process of testing the car to ensure that the car has met the goals set early on in design. This let us verify that all the design decisions made could be linked to overall vehicle goals
Safety management is also an incredibly important part, especially as a team transitioning to an EV platform, where safety risk goes from relatively minimal to something where significantly more caution is required. With SOPs, training, and certification we were able to document access to certain machines and parts to minimize risk
Pneumatic Shifting
Starting in my freshman year, I developed the design for a pneumatic shifting system. The first task involved researching the required components to achieve targeted shift forces and shifting count. Working with multiple other senior members I was able to come up with an initial design.
This design, while flawed, was a step in the right direction. Some key points that have been improved upon for the system that will be installed on our 2023 car versus the system that was designed for the 2022 car are the electrical board moving from an isolated board designed by me to a board designed in collaboration with the electronics subteam that handles both shifting and data logging. Another key improvement was the mounting, from a vehicle-mounted piston to a self-contained system entirely mounted on the engine.
The initial built design, while operable didn’t have enough shifts and struggled with consistency. Recalculating using different resources & with testing, the tank and piston were both upsized. These systems were then tuned, to a point where the drivers felt that they were a huge leap forward. Driver feedback is a massive indicator of an ergonomic system such as shifting, and all of the competition drivers felt that the effect of it was hugely positive.
At the competition, the shifting system ran without flaws during all dynamic events, although had a relatively major failure in the pneumatic regulator after autocross, the evening before endurance. The failure was traced to be likely due to repeated heating on a component not properly designed for the environments to which it was exposed. We were able to find a local paintball shop that had the part which enabled us to run in competition, scoring us a team-best result of 10th place out of 120 teams.
Driver Safety & Cockpit
For Mk. 8 I took up work on the driver safety design, focusing on making the CAD designs manufacturable. I also had to gain a deeper grasp of the rules and requirements for the safety systems on the vehicle. The main part I adapted towards manufacturability was the firewall, which required near ground-up design using sheet metal CAD, to then be adaptable to multiple manufacturers’ bend specifications. I had to redesign this multiple times, because of unconsidered rules by the engineer who originally designed the system, coming up with a system that was praised by technical inspectors for how simple it was
I also worked with wheels & steering and the drivers to spec a steering wheel and design the mounts for the shift paddles to integrate back into the shifting subsystem.
California teams at 2023 Competition
Prepping Mk8 for acceleration event at 2023 Competition
Mk8 at Willow Springs Test
Mk7 team photo at Willow Springs test
Pushing Mk7 at 2022 Competition
Mk7 Prep at SoCal Shootout 2022
Mk7 wing photo at 2022 SoCal Shootout
Mk7 Full Team Photo at 2022 Competition
Team working on Mk 9 at technical inspection
Mk9 at 2024 competition, on stands in pit
Mk9 on stands at the shop during integration effort